Understanding the Fundamentals and Applications of Plastic Extrusion in Modern Production
In the world of modern-day manufacturing, the strategy of plastic extrusion plays a crucial function - plastic extrusion. This intricate procedure, involving the melting and shaping of plastic with specialized dies, is leveraged across various markets for the creation of varied products. From car parts to customer products product packaging, the applications are large, and the potential for sustainability is similarly outstanding. Untangling the basics of this process reveals real convenience and capacity of plastic extrusion.
The Fundamentals of Plastic Extrusion Process
While it may appear complex, the principles of the plastic extrusion procedure are based on relatively uncomplicated concepts. It is a manufacturing process in which plastic is melted and then formed right into a constant profile via a die. The plastic extrusion procedure is thoroughly utilized in various markets due to its effectiveness, cost-effectiveness, and convenience.
Different Kinds Of Plastic Extrusion Strategies
Structure upon the fundamental understanding of the plastic extrusion process, it is necessary to discover the different techniques involved in this production technique. Both main techniques are profile extrusion and sheet extrusion. In account extrusion, plastic is thawed and formed right into a continual profile, usually utilized to produce pipelines, poles, rails, and window frameworks. On the other hand, sheet extrusion creates huge, flat sheets of plastic, which are normally further refined into products such as food product packaging, shower drapes, and vehicle components. Each method calls for specialized machinery and precise control over temperature and stress to guarantee the plastic preserves its form throughout air conditioning. Understanding these strategies is key to using plastic extrusion properly in modern manufacturing.

The Duty of Plastic Extrusion in the Automotive Market
An overwhelming majority of components in contemporary vehicles are items of the plastic extrusion procedure. This process has revolutionized the automobile industry, changing it into a more efficient, affordable, and flexible manufacturing sector. Plastic extrusion is primarily made use of in the manufacturing of different vehicle parts such as bumpers, grills, door panels, and dashboard trim. The procedure offers an attire, constant outcome, enabling suppliers to create high-volume parts with wonderful accuracy and minimal waste. The lightness of the extruded plastic components adds to the general decrease in car weight, boosting fuel effectiveness. Furthermore, the durability and resistance of these parts to warmth, cold, and effect boost the durability of autos. Therefore, plastic extrusion plays a crucial role in auto see page manufacturing.
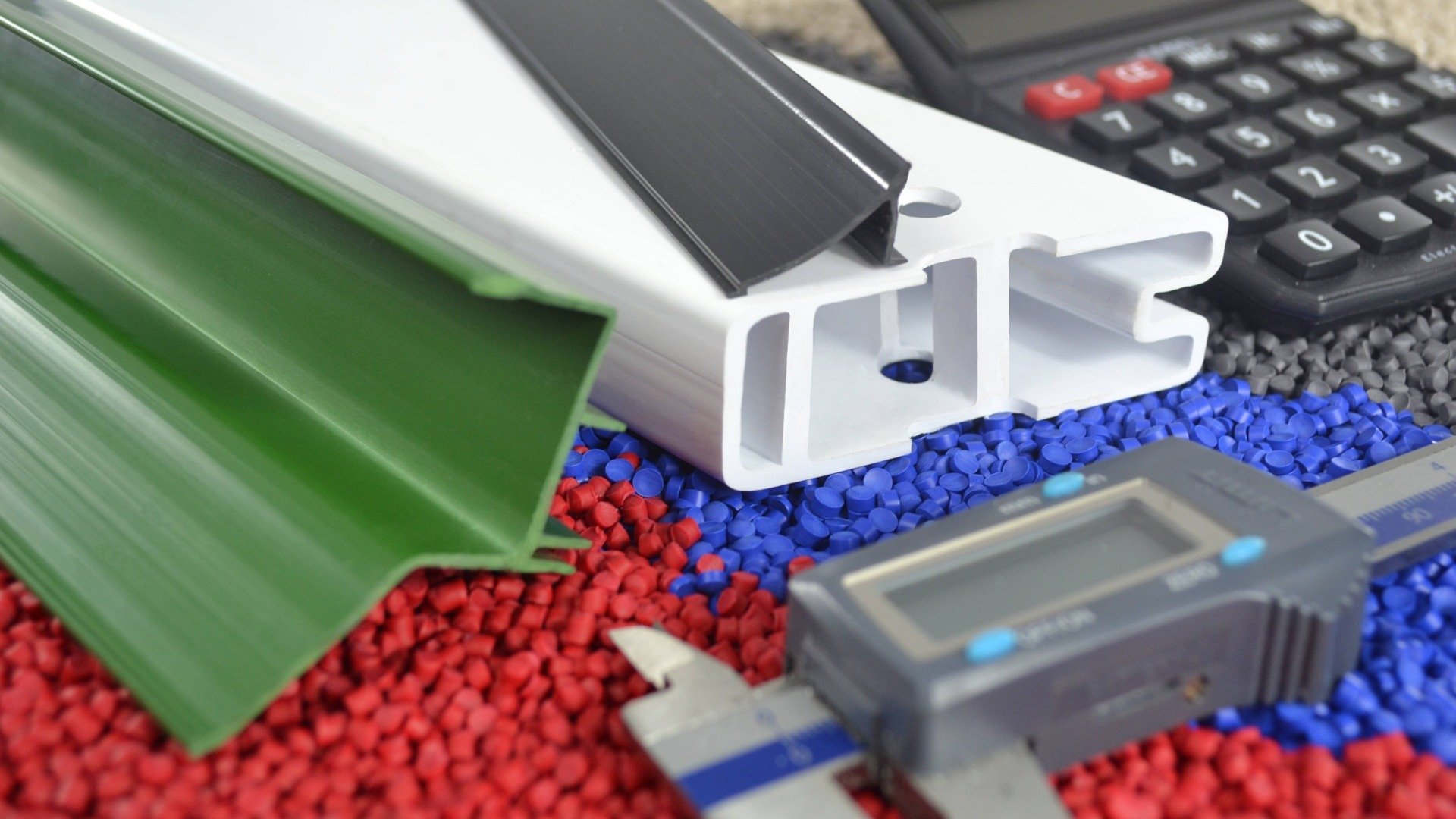
Applications of Plastic Extrusion in Consumer Product Production
Beyond its considerable impact on the vehicle sector, plastic extrusion shows just as effective in the realm of customer goods producing. The versatility of plastic extrusion enables manufacturers to develop and generate complex shapes and dimensions with high accuracy and efficiency. The versatility, adaptability, and cost-effectiveness of plastic extrusion make it a favored option for many consumer products suppliers, contributing substantially to the sector's development and development.
Environmental Effect and Sustainability in Plastic Extrusion
The prevalent use of plastic extrusion in manufacturing welcomes examination of its environmental implications. Efficient equipment minimizes energy usage, while waste administration systems recycle scrap plastic, decreasing raw material demands. Regardless of these enhancements, even more development is needed to mitigate the environmental footprint of plastic extrusion.
Final thought
To conclude, plastic extrusion plays a vital role in modern-day manufacturing, specifically in the vehicle and consumer products sectors. Its adaptability enables the manufacturing of a wide variety of parts with high precision. In addition, its capacity for reusing and development of eco-friendly materials uses a promising opportunity towards sustainable techniques, thus resolving environmental worries. Comprehending the essentials of this process is crucial to maximizing its benefits and applications.

The plastic extrusion procedure is thoroughly utilized in different markets due to look here its flexibility, effectiveness, and cost-effectiveness.
Building upon the fundamental understanding of the plastic extrusion process, it is required to explore the numerous strategies included in this manufacturing approach. plastic extrusion. In comparison, sheet extrusion produces large, level sheets of plastic, which are usually further processed right into products such as food product packaging, shower drapes, and automobile parts.A frustrating bulk of parts More Help in modern lorries are products of the plastic extrusion procedure
Comments on “Plastic extrusion for extra-durable, resilient materials”